Design Freedom, Anywhere
Achieve the look of full bed masonry on walls or ceilings — indoors or out — with versatile thin architectural stone options, compatible with adhered, tie & clip, or Fast Track™ systems.
Fast Track System™ = Fast Savings
No concrete footing required. The lightweight, pre-engineered Fast Track System™ simplifies installation, reduces structural demands, and cuts overall costs.
Sustainable by Design
Support your LEED goals with a system made from at least 25% post-consumer recycled aluminum. The Fast Track System™ is fully reusable — adaptable for future building needs.
Our Colors
Monotone Colors
Blended Colors
BUR RIDGE
A warm, natural blend of Oyster and Blush colors with soft beige and sandy tan hues.
Request Your Color Kit Today!
Looking for dependable color options that make selection easy?
Our Color Kit features clean, standard monotone tones that deliver timeless style and reliable consistency.
Design with Confidence
See and feel our standard monotone color options in person—ensuring accurate selections that align with your design vision and client expectations.
Enhance Presentations & Client Meetings
The Color Kit is a professional, tangible tool to support concept boards, material presentations, and on-site consultations.
Informed Specifications
Make faster, more precise material selections backed by real samples—streamlining the specification and approval process.
Organized & Office-Ready
Compact, clean, and easy to store—an essential addition to your materials library or sample room.
Custom Color Matching
At Reading Rock, we excel in custom color matching, ensuring our RockCast blends seamlessly with existing materials. Unlimited color options available that are sure to meet any design requirement.
The Right Color Everytime!
Seamless Integration
RockCast’s custom color matching ensures a perfect fit with existing materials.
Unlimited Color Options
Choose from a vast range of hues or create a custom blend.
Advanced Manufacturing
Consistent, high-quality color production for every project.
Architectural Versatility
Designed to complement diverse styles and materials.
Textures
From sleek, smooth finishes to bold split-face styles, our Thin Stone Series offers a range of textures — including smooth, chiseled, and split — to complement any design vision.
Sizing
Smooth 7⁄8" Bed Depth
Chiseled 7⁄8" Bed Depth
Chiseled ST-203-8610
(D) 1 3⁄4" x (H) 11 5⁄8" x (L) 23 5⁄8"
Mortar bed depth 7⁄8", total depth 1 3⁄4"
Smooth 1 3⁄16" Bed Depth
Split-Face 1 3⁄16" Bed Depth
Cut Options
We offer a variety of cut options to keep your project moving efficiently—saving you time, labor, and headaches on the job site.
Installation Options
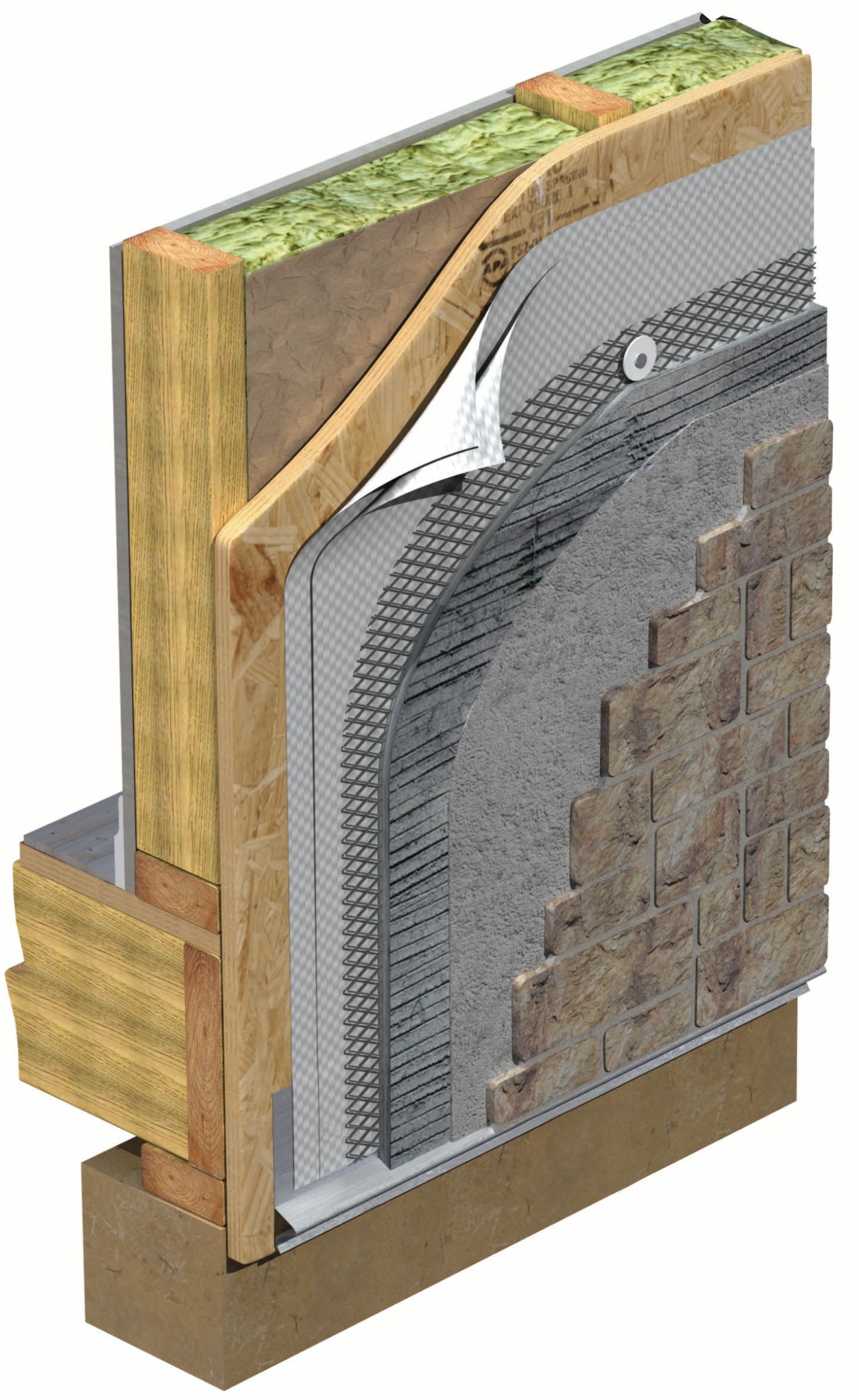
Adhered System
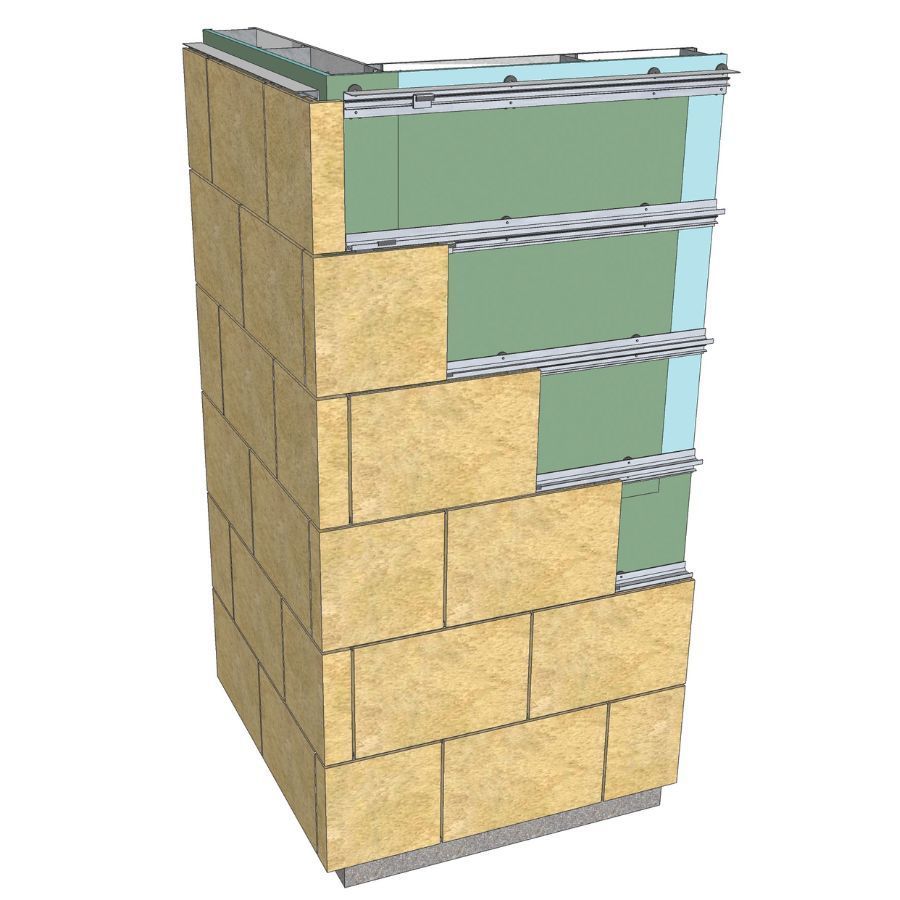
Fast Track System
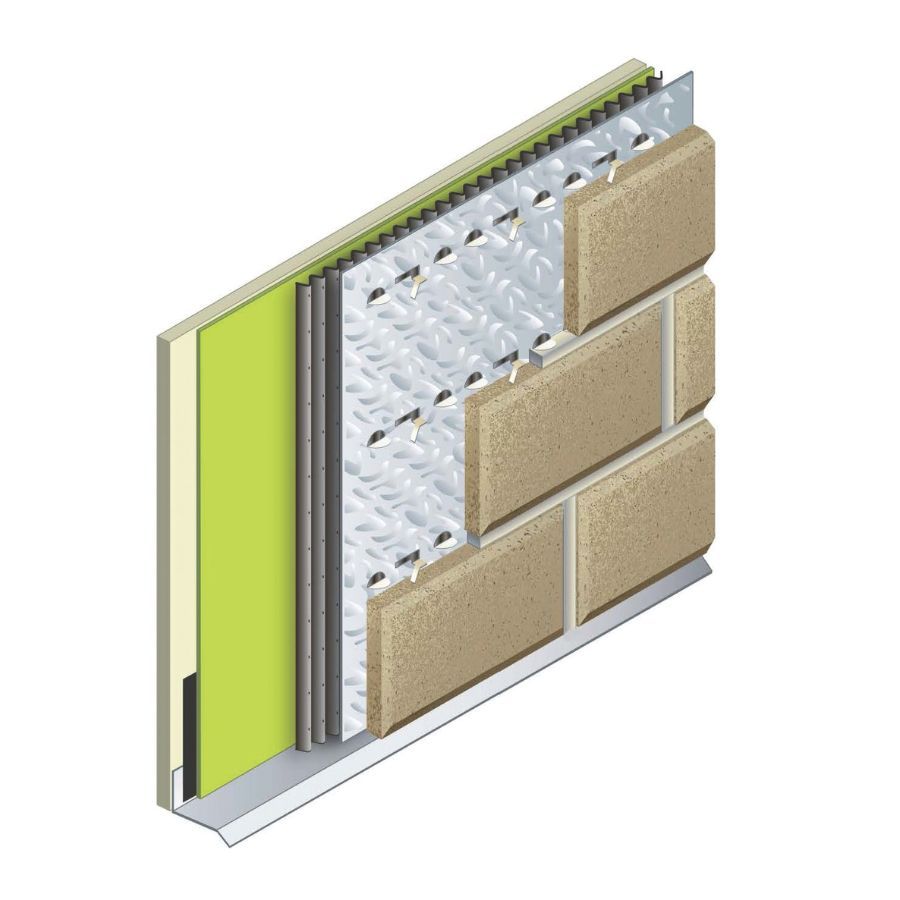
Tie & Clip Support Panel System
Track Options
Our Process: Quality at Every Step
We don’t leave anything to chance. At Reading Rock, we control every step of the process to ensure top-quality products, fast turnaround, and reliable delivery.
Step 2:
Precision Manufacturing
From the careful selection of raw materials to the final product, our experienced team monitors every stage of production for consistency and durability.
All Reading Rock manufacturing facilities are certified by the NPCA, meeting the highest standards for plant facilities, production, and quality control procedures.
Our cast stone products undergo rigorous examination of product quality, safety, testing, and meticulous record-keeping certified by the Cast Stone Institute (CSI)
Guidelines and Specs
Need Help with Your Architectural Masonry Veneer Project?
Contact Us
Have questions about product details, ordering, or installation? Our team is here to assist you at every stage of your project. Whether you’re selecting the right textures and colors or need expert advice on design and application, we’re ready to help.